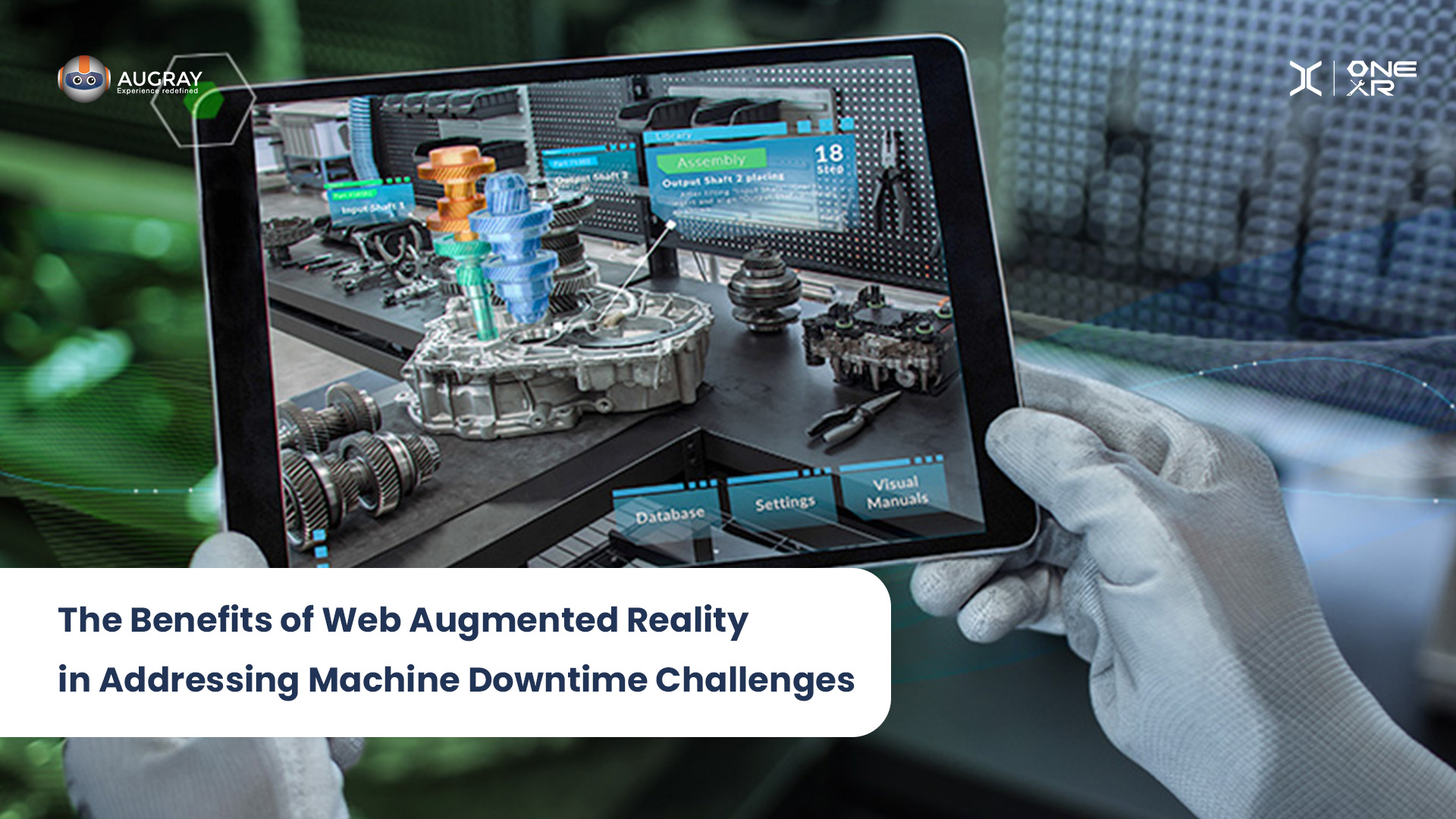
Web Augmented Reality (WebAR) has gained significant attention in recent years for its potential to revolutionize various industries, including manufacturing and maintenance.
When it comes to addressing machine downtime challenges, WebAR offers several benefits that can help streamline maintenance processes, improve efficiency, and minimize costly downtime. Here are some key advantages of using WebAR in tackling machine downtime challenges:
- Real-time Visualization: WebAR enables technicians to overlay digital information, such as maintenance instructions, schematics, or error codes, onto the physical equipment they are working on. This real-time visualization helps technicians quickly understand complex systems and troubleshoot issues effectively, reducing the time spent on diagnosing problems.
- Remote Assistance: WebAR allows remote experts to provide guidance and support to onsite technicians in real-time. Using a web browser and a compatible device, remote experts can connect with onsite personnel, view the machine through their device’s camera, and overlay instructions or annotations onto the live video stream. This capability is particularly valuable when faced with complex issues that require specialized knowledge or when experts are located far away, eliminating the need for travel and reducing downtime.
- Training and Onboarding: WebAR can play a crucial role in training new technicians or upskilling existing ones. By leveraging augmented reality, training modules can be created to provide immersive and interactive experiences, allowing technicians to practice maintenance procedures in a virtual environment. This helps reduce the learning curve and enables technicians to quickly become proficient in handling various equipment, leading to faster issue resolution and minimized downtime.
- Remote Monitoring and Predictive Maintenance: WebAR can be integrated with Internet of Things (IoT) devices and sensors to enable real-time monitoring of machine performance. By visualizing sensor data and analytics in an augmented reality overlay, technicians can gain insights into the health of the equipment, identify potential issues, and proactively schedule maintenance activities before a breakdown occurs. This predictive maintenance approach helps prevent unplanned downtime and extends the lifespan of machinery.
- Documentation and Collaboration: WebAR facilitates the creation and sharing of comprehensive documentation for maintenance procedures. Technicians can capture images, videos, and annotations directly within the augmented reality environment, documenting the steps they take, any modifications made, or issues encountered. This documentation can be easily shared with other team members, providing a valuable knowledge base for future troubleshooting and reducing the time needed to resolve similar issues.
- Cost and Time Savings: By leveraging the benefits mentioned above, WebAR helps reduce machine downtime, improve maintenance efficiency, and minimize travel expenses for expert assistance. This leads to substantial cost savings for organizations, as they can avoid prolonged downtime and quickly address issues without waiting for specialized technicians to arrive onsite.
Web Augmented Reality (WebAR) has been implemented in various industries to address machine downtime challenges. Here are some real-life examples of how WebAR has been used in this context:
- Automotive Manufacturing: Automotive companies have utilized WebAR to streamline maintenance and repair processes. For example, technicians can use WebAR to overlay digital instructions and 3D models onto physical car components, enabling them to quickly identify and resolve issues during assembly or repair. This reduces downtime and improves the efficiency of maintenance operations.
- Aerospace Maintenance: Aircraft maintenance involves complex systems and requires specialized knowledge. WebAR has been employed to provide remote assistance to technicians during aircraft maintenance and repairs. Experts can connect with onsite technicians using WebAR platforms, view the aircraft through the technicians’ devices, and overlay instructions or annotations to guide them through complex procedures. This real-time collaboration helps minimize downtime and ensures accurate repairs.
- Industrial Machinery Maintenance: WebAR has been applied in the maintenance of large industrial machinery. Technicians can use WebAR to visualize equipment components, access maintenance manuals or schematics, and follow step-by-step instructions overlaid onto the physical machine. This enhances their understanding of the machinery and accelerates troubleshooting and repair processes, reducing downtime significantly.
- Medical Equipment Maintenance: Hospitals and healthcare facilities have adopted WebAR for maintenance tasks on medical equipment. Technicians can use WebAR to access digital manuals, repair guides, and equipment schematics, which can be overlaid onto the physical equipment through the device’s camera. This helps technicians quickly identify and resolve issues, minimizing downtime for critical medical devices.
- Power Plant Maintenance: Power plants require regular maintenance to ensure smooth operation. WebAR has been employed to assist technicians in power plant maintenance tasks. They can use WebAR to access real-time sensor data, visualize equipment performance, and overlay diagnostic information on the physical machinery. This enables technicians to identify potential problems, schedule maintenance activities, and prevent unexpected downtime.
- HVAC System Maintenance: Heating, ventilation, and air conditioning (HVAC) systems are crucial for maintaining a comfortable environment in buildings. WebAR can be utilized to enhance maintenance procedures for HVAC systems. Technicians can access digital documentation, maintenance checklists, and interactive 3D models overlaid onto the physical equipment. This helps them diagnose and resolve issues efficiently, reducing downtime and improving system performance.
Here are some specific examples of how web AR is being used to address machine downtime challenges:
- Siemens is using web AR to help its customers troubleshoot and repair industrial machines. The company’s AR app provides technicians with real-time instructions and guidance, as well as access to a library of spare parts.
- Bosch is using web AR to train its employees on how to use its industrial machines. The company’s AR app provides employees with a virtual simulation of the machines, which they can use to practice their skills without having to risk damaging a real machine.
- GE is using web AR to help its customers improve the efficiency of their manufacturing processes. The company’s AR app provides customers with real-time data on their production lines, which they can use to identify and address problems.
These real-life examples highlight the practical application of WebAR in addressing machine downtime challenges across various industries. These are just a few examples of how web AR is being used to address machine downtime challenges. As the technology continues to develop, we can expect to see even more innovative and effective ways to use AR to improve the performance of industrial machines.
In conclusion, Web Augmented Reality offers a range of benefits in addressing machine downtime challenges. By providing real-time visualization, remote assistance, training capabilities, predictive maintenance, documentation, and cost savings, WebAR empowers technicians with enhanced tools and knowledge to diagnose, repair, and maintain machinery efficiently, improving overall operational efficiency and reducing downtime.