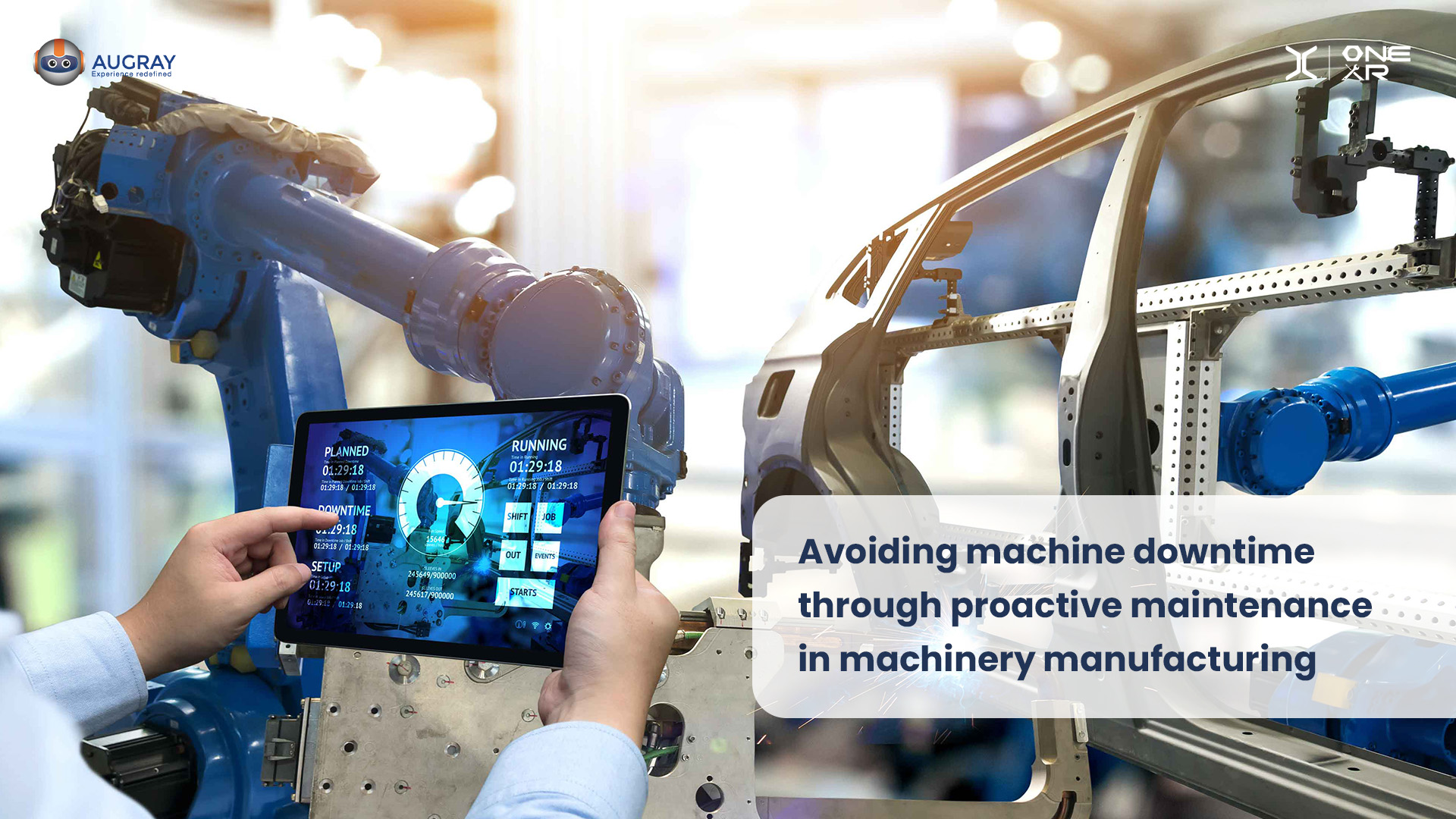
Introduction:
In the fast-paced world of machinery manufacturing, minimizing machine downtime is crucial for maintaining productivity and ensuring efficient operations. Downtime not only leads to lost production and revenue but also disrupts supply chains and customer satisfaction.
In this blog, we will explore the concept of proactive maintenance and how it can help prevent machine downtime. Additionally, we will delve into the role of Augmented Reality/Virtual Reality (AR/VR) in enhancing proactive maintenance practices. Let’s dive in!
Understanding Machine Downtime and its Impact:
- Machine downtime refers to the period during which a machine is not operational, leading to a halt in production. The consequences of machine downtime can be far-reaching, impacting several aspects of machinery manufacturing:
- Production Losses: When machines are not running, production targets are not met, resulting in a direct loss of output. This can lead to delayed deliveries, increased backlogs, and dissatisfied customers.
- Revenue Impact: Reduced production directly affects revenue generation, as the manufacturing process is unable to fulfill customer orders in a timely manner. Moreover, the costs associated with unscheduled repairs can further erode profitability.
- Maintenance Expenses: Reactive maintenance, which involves fixing machines after they break down, often incurs higher costs due to emergency repairs, expedited spare part orders, and overtime labor. These expenses can be significantly reduced through proactive maintenance strategies.
Causes of Machine Downtime:
To effectively tackle machine downtime, it is essential to identify its underlying causes. Here are some common reasons for machine downtime:
- Mechanical Failures: Components and parts can wear out, resulting in breakdowns. Lack of proper lubrication, loose connections, and misalignment are common mechanical issues that can lead to downtime.
- Electrical and Control System Failures: Faulty wiring, blown fuses, and malfunctioning sensors or controllers can cause machines to stop functioning.
- Lack of Preventive Maintenance: Neglecting regular maintenance tasks such as cleaning, inspections, and calibration can lead to premature equipment failure and unplanned downtime.
Proactive Maintenance: Preventing Downtime Before It Occurs:
Proactive maintenance involves taking pre-emptive measures to prevent machine downtime rather than reacting to failures after they happen. This approach is based on systematic inspections, preventive maintenance schedules, and the use of advanced technologies to monitor equipment health. Here’s how proactive maintenance helps in avoiding downtime:
- Regular Inspections: By conducting periodic inspections, manufacturers can identify potential issues and address them before they result in breakdowns. This includes checking for wear and tear, verifying proper lubrication, and detecting any signs of imminent failure.
- Scheduled Maintenance: Establishing a proactive maintenance schedule ensures that machines are regularly serviced, calibrated, and updated according to manufacturer recommendations. This reduces the likelihood of unexpected failures and extends the lifespan of equipment.
- Condition Monitoring: Leveraging sensor technology and data analytics, manufacturers can monitor the condition of critical machine components in real-time. This allows for early detection of anomalies and proactive intervention before a breakdown occurs.
The Role of AR/VR in Proactive Maintenance:
Augmented Reality (AR) and Virtual Reality (VR) technologies are revolutionizing the way proactive maintenance is performed in the machinery manufacturing industry. Here’s how AR/VR can enhance maintenance practices:
- Training and Skill Development: AR/VR platforms provide immersive and interactive training environments where technicians can learn maintenance procedures, troubleshoot equipment, and practice complex repairs. This reduces training time and improves the effectiveness of maintenance personnel.
- Remote Assistance: AR/VR enables remote experts to provide real-time guidance to on-site technicians. By overlaying digital instructions and annotations onto live video feeds, remote experts can assist with troubleshooting, reducing the need for travel and minimizing downtime.
- Predictive Maintenance Visualization: AR/VR can visualize real-time sensor data and equipment performance metrics, allowing maintenance personnel to identify patterns and predict failures. This enables proactive interventions and helps prevent unexpected downtime.
Conclusion:
Minimizing machine downtime is crucial for machinery manufacturers to maintain productivity, reduce costs, and enhance customer satisfaction. By adopting proactive maintenance strategies and leveraging AR/VR technologies, manufacturers can detect potential issues early, prevent breakdowns, and optimize their maintenance practices.
Investing in proactive maintenance not only ensures smoother operations but also provides a competitive advantage in an industry driven by efficiency and reliability.
Remember, proactive maintenance is a continuous process that requires commitment and collaboration across all levels of the organization.
By prioritizing proactive maintenance practices, manufacturers can significantly reduce downtime, increase equipment lifespan, and achieve long-term success in the machinery manufacturing industry.